GRANULATION LINE
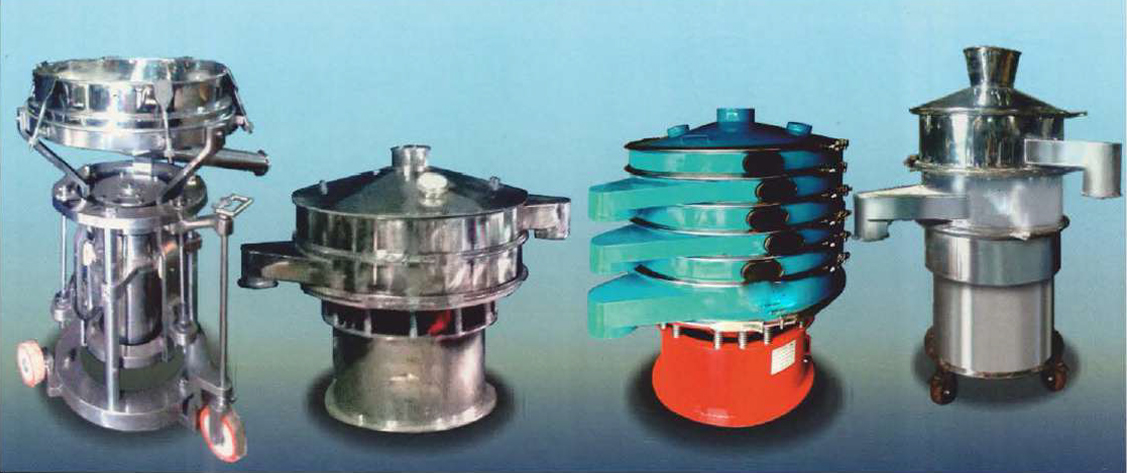
MECHANICAL SIFTER AND VIBRO SIFTER
We offer top-class vibro sifters that are circular gyratory screens, vital to separate solids from solids and liquids from solid. Our range is available in different diameters of 20”, 30 “, 36” & 48” . We can also customize our vibro sifters as per the client’s requirements. Some of the salient features of our vibro sifter encompass of the following
Faster separation, Process adaptability, Long screen life lesser maintenance and power consumption than conventional sifters high capacity and optimum use of space Widely demanded worldwide, our vibro sifter has following special attributes as well Stainless steel GMP construction with S.S.304 or 316 contact parts.
Faster output at low power consumption, Double deck arrangement can be provided. Fitted with Vibro Motor Provded lid for dust free operation.
PASTE KETTLE
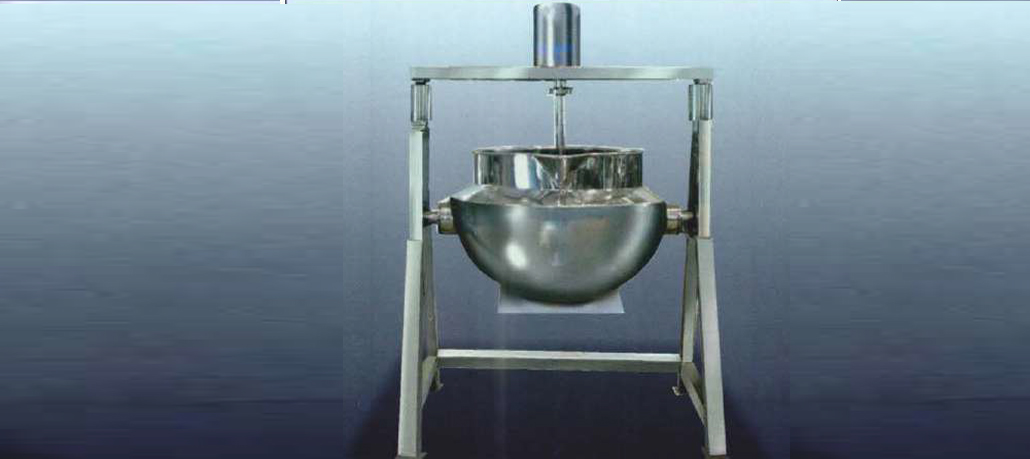
The tilting paste kettle, is designed for paste preparation. It has
a universal applicaton resulting in uniform melting. This tank is
designed to meet missing needs of wider range of products under
varied operating conditions in Chemicals, Foods, Cosmetics and
Pharmaceutical Industry.
The basic principle utillized in the design of this kettle is the jacket
for passing steam n order to melt down the product to make paste.
This kettle has an unique tilting arrangement for discharging the
product.
MULTIMILL
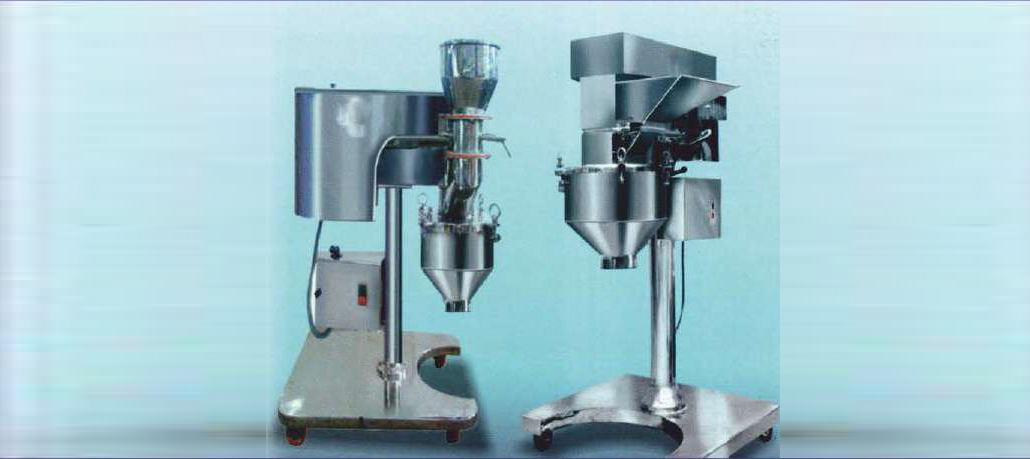
Multimill is used for wet granulation, pulverization in pharma & chemicals industries it operates on the principle of variable force swing beaters having both knife & impact edges rotating within a selected screen to get the required size reduction. Material fed in the hopper passes down to the processing chamber wherw it moves to the periphery and passes through the screen radially and tangentially. Finally the processed material gets collected in the c on tainer kept blow the processing chamber.
RAPID MIXER GRANULATORS
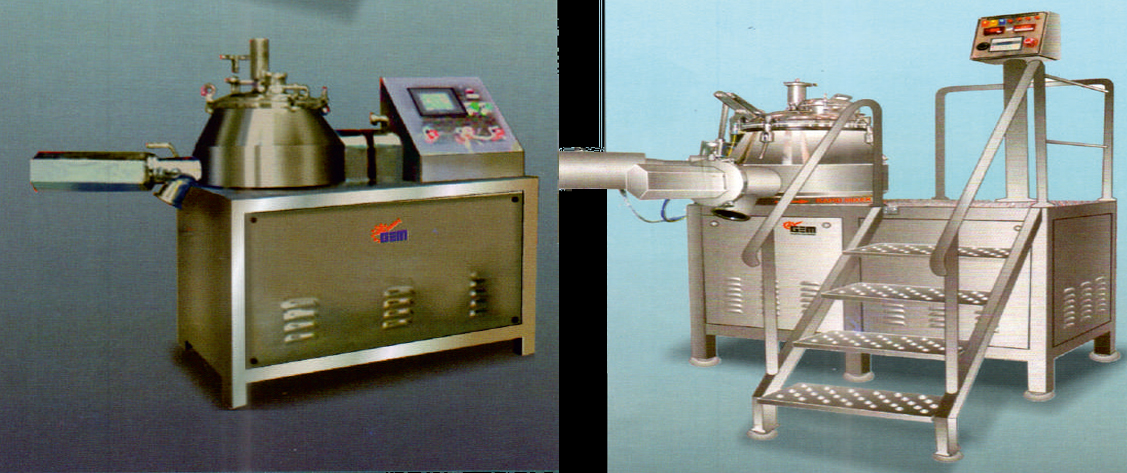
NITIN Rapid Mixer Granulators are specifically designed to efficient mixing amd wet granulation of powders, provided consistence quality. These mixer offer a wide range of features for raw material and binder charging, variants for setting up, cleaning & automation controls apart from direct connections to the vent mill & down steam process such as Fluid Bed Drying the highest cGMP standards. The rapid mixer granulator is the result of deep knowledge of the specific requirements of solid dosage processing in the pharma industries.
FEATURES
BOWL
SS 316 construction with cylindrical design and conical top for optimum mixing. Effective mixing even with Lightly difficult material. Provided with Quick acting clamps for the locking. Lid interlock for operator safety. Vent lifter is provided at the top of lid.
CHOPPER
4 Blade chopper SS 316 construction has high surface area for lumps breaking for compaction of proper granules. Mounted of the wall of the bowl horizontally with sealing. Proper purging through air to avoid power entering in to shaft and at the same time maintaining cooling to the shaft.
IMPELLER
3 Blades impeller, SS 316 construction tangentially attach. Proper sealing is provided to prevent leakage. Blades enlarge at end to maximum product. Minimum bottom and wall clearance for maximum product yield.
PURGING SYSTEM
A pneumatic regulator with gauge provided for chopper & impeller to prevent lealage of water entering into shaft. Discharge pneumatically operated easier to discharge material into the container with to and fro motion.
INTERLOCKS
- For Lid.
- Impeller to chopper.
- For discharge of material.
- FBD container present or not unless the FBD bowl present at the discharge gate, material will not be discharged.
- Low air pressure and purging pressure interlock.
- Distilleries and allied
OPTION
CIP systems: Comprises of pump, Spray Ball Spray Nozzle with T. C.End. /PLC
FLUID BED DRYER
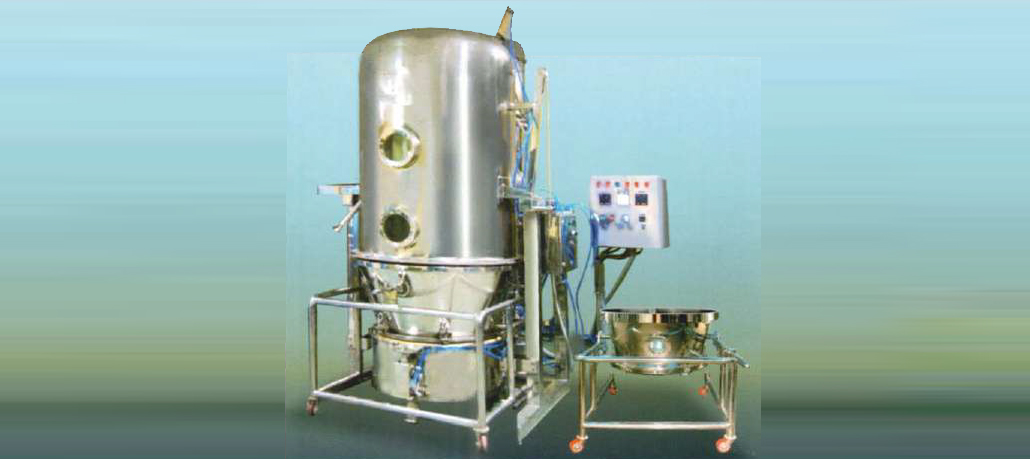
NITIN Fluid Bed Dryer is used for processing of various minerals and chemicals in the Pharmaceutical industry. Our fluid bed dryer consists of a simple drying unit and helps in the conversion to a granullation or coater when optional packages are incorporated. dryers are available in standard pneumatic logic and sophisticated computerized controls and are also offered in Steam heated Model. Our dryers provide simple solution to dry products and are high in performance
- cGMP standard constructed in 2 bar pressure.
- AHU & Exhaust blower, AHU comprises of pre-filter, Micro VEE and HEPA filter.
- PC satin cloth for filter bag, Sampling port, Illumination lamp, Explosion vent, Iinflatable seal will be provided.
- Standard Auto Control System.
- Capacity ranges from 1 Kg to 350 Kg
TRAY DRYER
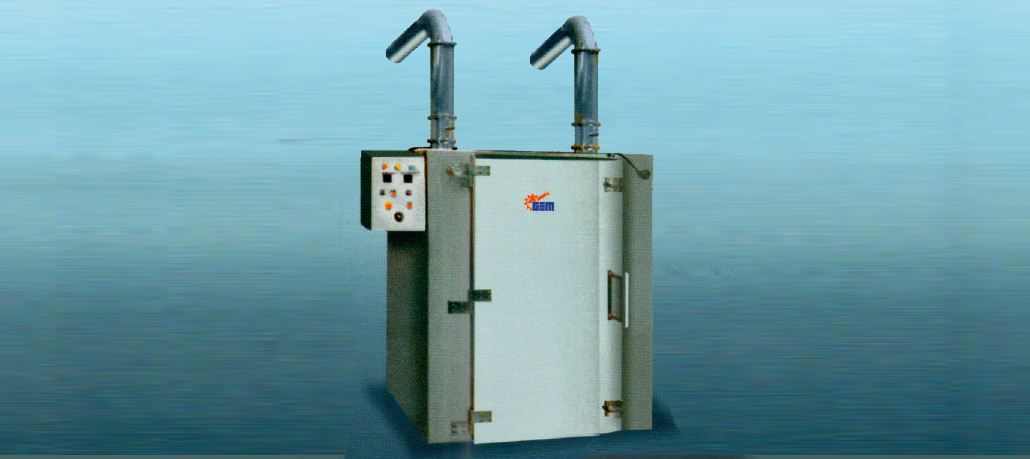
GEM Tray Dryer is the most conventional dryer used very widely and still being used where the moisture content is more and where the product has to be dried at low temperature for long hours. It can be electrically heated or Steam heated Tray dryer making with 6, 12, 24, 48, 96 and 192 trays. It can be inside outside MS or GMP model depending upon the product and industry requirement.
Construction : 3mm thick sheet & suitably with angles and sections. The dryer’s external walls are from 1.6 mm SS of 304 qualities. The internal of the dryer is built of 1.6 mm thick SS 304 sheets. It is insulated with 50 mm thick glass wool insulation and Cladded with SS Polished sheets. Door lips- Neoprene rubber Gasket. Trays from 1.6 mm SS 304 with round corners, Mirror finish SS 316 quality is available on demand.
VACUUM TRAY DRYER
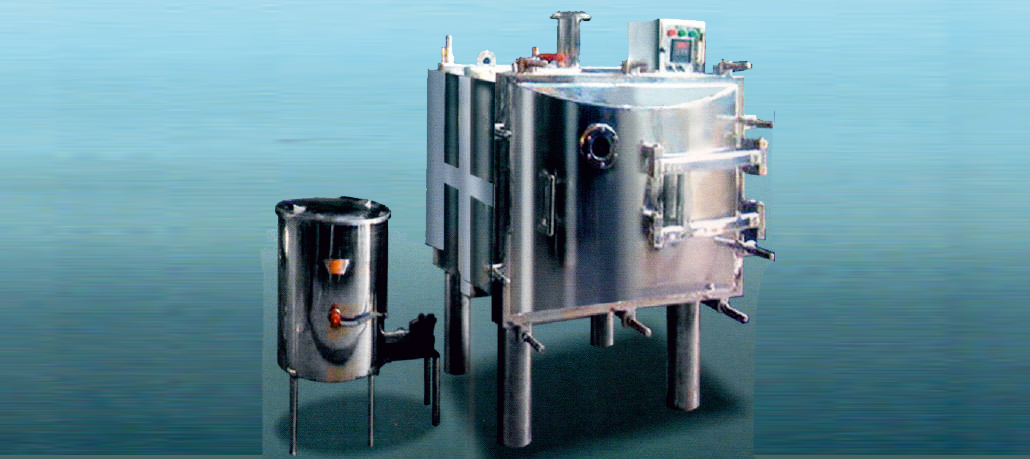
Main Body/Vacuum chamber thick SS 316 Plate with heavy duty SS 316 flange and stiffeners. Door SS 316 plate (Hemisphere shape) SS 316 flange. Shelves hollow type pads with SS 316 sheet and baffles. Condenser (shell & tube) & receiver SS 304 with isolation valve and flow glass in between to monitor condensation. Trays in SS 316 rounded corners and edges. Explosion vent/ rupture disc on vacuum chamber.Pressure release valve in steam line.
Provided On :View and light glass vacuum chamber door, Silicon gasket for door and Nitrogen purging & Vacuum break valve on vacuum chamber.
Optional : Hot water system (steam heated) with MS tank (insulated), SS 304 steam radiator/electrical heater, Circulation pump with FLP motors and controls. Vacuum Pump (2 stage water ring) with FLP motor.